Chemical Engineering Research and Laboratories
Research
UTC's Chemical Engineering program is one of the most comprehensive and well-rounded chemical engineering programs available. The program emphasizes applying theoretical knowledge to practical problems, in order to prepare students for a career in chemical engineering. UTC's faculty are recognized and renowned engineers in the field, and they're committed to sharing their experience with UTC students. For example, many of UTC’s chemical engineering faculty have received funding through national and government organizations. UTC’s MS in Chemical Engineering is accredited by ABET, ensuring that it meets the highest standards of quality and excellence. Graduates of UTC's Master's in Chemical Engineering program are highly sought after by employers, making it one of the most valuable degrees you can earn.
Faculty Research Areas

Dr. Bradley Harris
Email: [email protected]
Research Areas:
- Identifying common pathways and mechanisms in bacterial disease pathogenesis
- Understanding how bacteria adapt to their environment through membrane remodeling
- Developing prevention and treatment strategies for bacterial diseases
- Using synthetic biology to build microbial cell factories
- Constructing renewable routes to energy and commodity chemicals

Dr. Sungwoo Yang
Email: [email protected]
Research Areas:
- Transparent insulating materials
- Lightweight thermal and electrical additives
- Modeling heat and mass transfer
- Solar thermal energy conversion
- Energy-efficient building
- Water harvesting
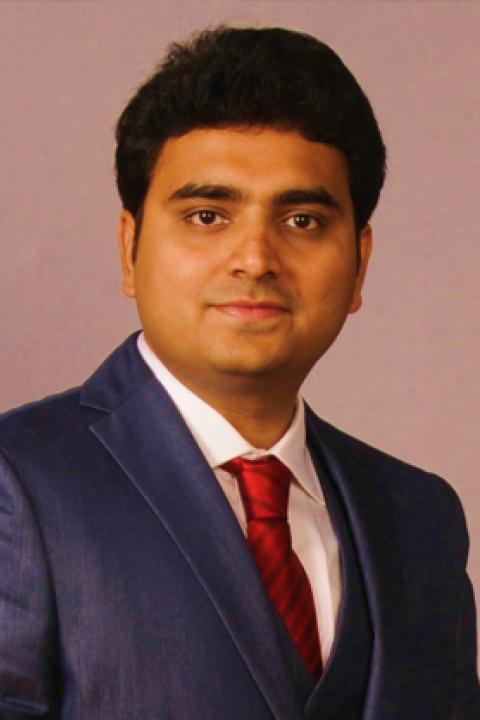
Dr. Rahul Bhosale
Email: [email protected]
Research Areas:
- Solar Thermal Processes and Alternative Fuels
- Thermochemical, Photochemical, and Electrochemical Processes
- Heterogeneous Catalysis and Advanced Materials
- Desalination and Wastewater Treatment
- CO2 Capture, Conversion, and Storage
- Bioenergy, Biofuels, and Bioproducts
- Thermal Energy Storage and Batteries
- Air Pollution Control and Solid Waste Treatment
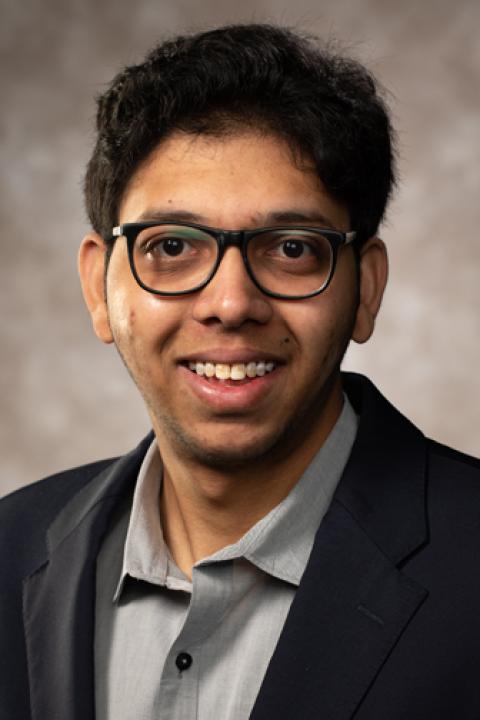
Dr. Venkateswara Rao Kode
Email: [email protected]
Research Areas:
- Boron nitride quantum dots synthesis, characterization and applications development
- Renewable water harvesting using 'green' solvents
- Direct air capture by sustainable bio-based sorbent materials
- Waste-derived polymer bionanocomposites for 3D printing applications
Laboratories
Dr. Frank Jones Chemical Engineering Research Lab (ECS 119)
This laboratory supports faculty and undergraduate research focused in two main areas: (1) design and construction of a chemical energy-powered car for the Chem-E-Car Competition sponsored by the American Institute of Chemical Engineers (AIChE); and (2) design and analysis of microreactors for the production of biorenewable fuels.
UTC’s nationally recognized Chem-E-Car team regularly competes in the AIChE regional and national competitions. This competition tests a team’s ability to engineer a chemically powered vehicle that will carry a given water weight for a given distance and stop using a carefully timed and calibrated chemical reaction. UTC’s Chem-E-Car team has qualified for nationals four times in the last seven years. These undergraduate students continually develop and assess new car designs, including exploring new power methods such as microbial fuel cells, chemical batteries, and biodiesel fuel. UTC’s continued success in this competition provides national and international recognition for the department, the college, and the university as a whole.
The current focus of the biorenewable fuels research is the production of biodiesel in a microreactor. In comparison to biodiesel production using batch reactors, these microreactors are able to convert reactants (triglycerides and methanol) to products much more quickly. This efficiency is largely due to the ease of diffusion and availability of catalytic surface provided by scaling down to such a small size. Additionally, the use of heterogeneous catalysis over homogeneous catalysis eliminates unwanted saponification of free fatty acids in the process, and can actually convert the free fatty acids to biodiesel.
Dr. Jim Henry Controls Systems Lab (ECS 120)
This laboratory supports the following: ENCH 3280L, Control Systems Laboratory; ENCH 3350, Unit Operations Laboratory; ENCH 4350, Chemical Processes Laboratory; and ENEV 4350, Environmental Processes Laboratory. It contains lab stations involving unit operations such as absorption, distillation, heat transfer, fluid flow, and reaction kinetics. This lab is under continued development for deployment as a remote laboratory through the use of Internet of Things (IoT).
There are four stations in this laboratory devoted to the unit operations and chemical/environmental processes labs. These include a packed bed absorption column and a twelve-stage distillation column, both of which span two floors. There is also a chemical reactor station for studying reaction kinetics in a continuous stirred tank versus a packed bed, as well as a heat exchanger station for studying heat transfer in a variety of heat exchanger configurations.
There are also three stations in this laboratory used in control systems lab. First is the cooling duct consisting of an air blower, duct work, and a thermal element. Secondly, there is a multi-tank level control system. The last station contains a simple pipe flow system with a water pump.
Other equipment housed here includes two fume hoods, a rotary evaporator, a Parr calorimeter, a spectrophotometer, and other equipment common to a wet chemistry lab.
Bioengineering Lab (ECS 441)
Research in this lab involves using the principles of biology and the tools of engineering to enable breakthroughs in biotechnology. Fields of application include disease treatment and prevention, environmental remediation, and renewable routes to energy and other chemical products. The bioengineering laboratory is furnished with a MilliQ Direct 16 water purification system; a New Brunswick BioFlo 3000 bioreactor equipped capable of temperature, pH, and dissolved oxygen concentration measurement and control; a Thermo Scientific 1300 Series Class II, Type A2 biological safety cabinet; and a Yamato SQ810C mobile autoclave with an 80 L capacity, capable of sterilization temperatures of up to 135°C. The lab also includes other equipment common to a wet biochemistry lab.
Recent projects include:
- Engineering unicellular green algae to overproduce triacylglycerides that can then be converted into biodiesel. There are three main thrusts to this project: (1) to develop a mutant algae strain that is optimized for TAG overproduction using metabolic modeling techniques, (2) cultivate the microalgae and isolate the TAGs, and (3) convert the TAGs into biodiesel and characterize its quality.
- Producing organic sweeteners from microbes as an alternative to chemical methods used currently. There are three main tasks: (1) engineer an optimal microbial strain using metabolic modeling, (2) cultivate the microbe and isolate and characterize the sweetener obtained, and (3) evaluate the economic feasibility of the full scale process.