Jason Heacker
A Study in Aerodynamic Drag Reduction for a Small Travel Trailer
Master of Science Degree in Engineering (concentration in Computational Engineering) Awarded Posthumously, University of Tennessee at Chattanooga
Jason A. Heacker, May 2011
It is well known that the engineering design cycle can be improved through the use of physics-based simulation. Performing simulations prior to making physical changes to a given design is advantageous because many design obstacles can be overcome without having to resort to “real world” (i.e., physical) testing. Instead, computational fluid dynamics (CFD) simulations were performed on a van, a small travel trailer, and on the van pulling the trailer where the overall goal of the analysis was to suggest various ways to reduce the aerodynamic drag of the van-trailer combination. The approach was to use the results of the simulations to separately analyze the aerodynamics of each geometry in order to better understand interference effects that the trailer has on the van and vice versa.
The first step of each of the three cases was to generate surface and volume grids for each geometry. Gridgen (a commercial software package for generating structured and unstructured grids) was used to create a database of grid files. The initial grids for all configurations were problematic because of the lack of resolution in regions of high gradients of the dependent variables. For example, initial attempts to generate viscous flow solutions using the SimCenter’s Tanasi software (using the incompressible flow assumption) were not successful except when first-order fluxes were used, even when executed using a unity CFL number. Reynolds numbers for the van, trailer and van-trailer combination were 8.3M, 12.6M, and 8.3M, respectively, all for air at sea level pressure at a temperature of 30°C. Also, initial simulations were executed using a “wind tunnel” frame of reference; that is, the bodies were taken to be stationary and the flow moves relative to the bodies. In this mode, the roadbed is stationary relative to the bodies, which is contrary to the actual case where the bodies move relative to the roadbed. Also, the tires were not rotating in the initial simulations. Fortunately, most grid issues were resolved to the point that second-order viscous solutions could be obtained. In addition, a moving ground plane and rotating tires were added to the simulations, thus allowing the computation of higher-order and more realistic solutions. Computations were then performed on the van-trailer combination using grids that were generated with all the key surfaces tagged separately to allow the drag components to be computed on various parts of the geometries; e.g., tires, A/C, trailer and van base, etc.
Tragically, Jason never got to perform the analysis to determine how the various drag components affected the overall configuration drag and therefore was not able to draw conclusions and make suggestions about how the configuration might be modified to minimize the drag. It is the hope of his friends at UTC and the SimCenter that this plaque will serve as a continuous reminder of Jason’s friendship, his curiosity, and his love of all things related to computing and computational engineering.
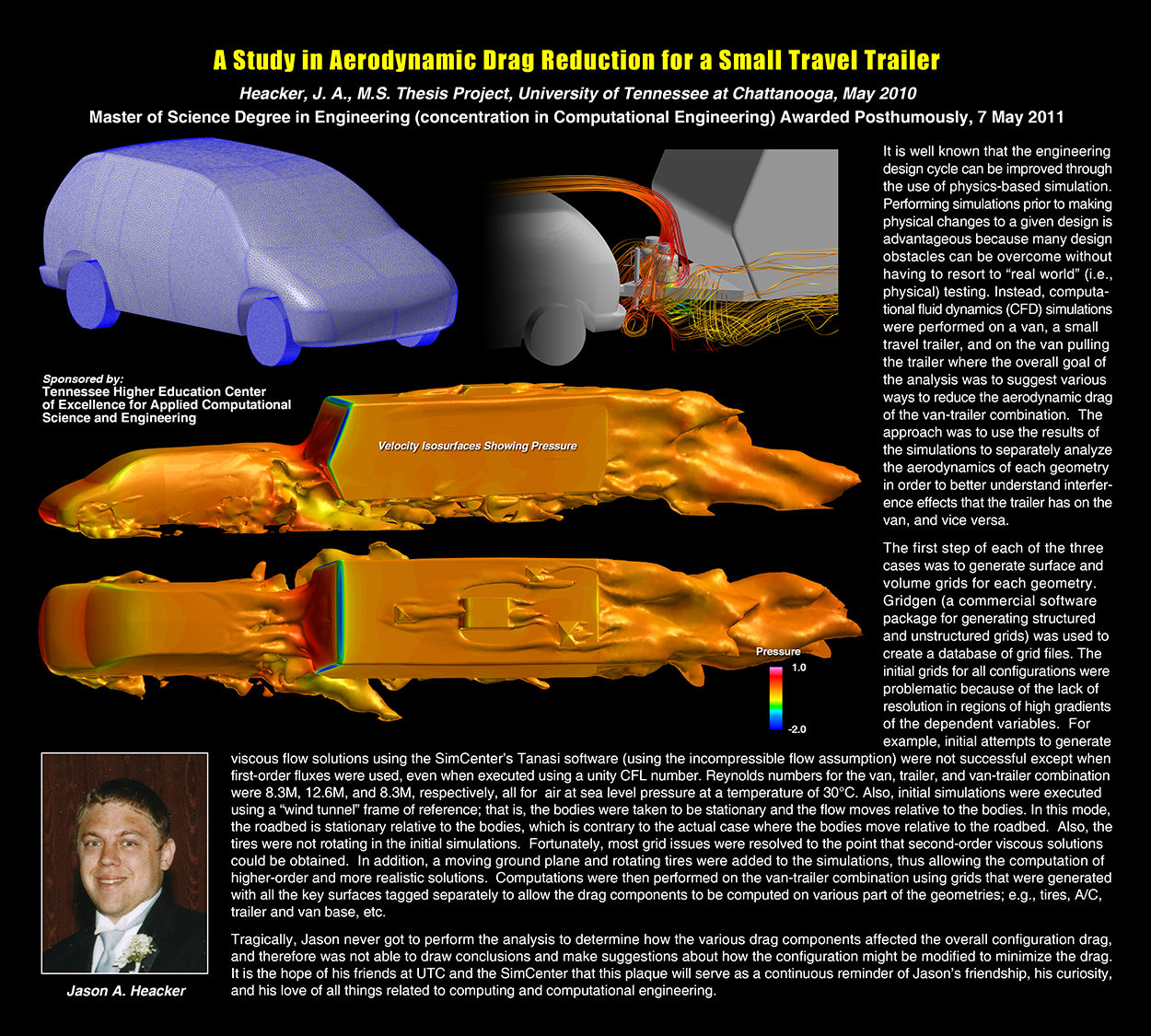